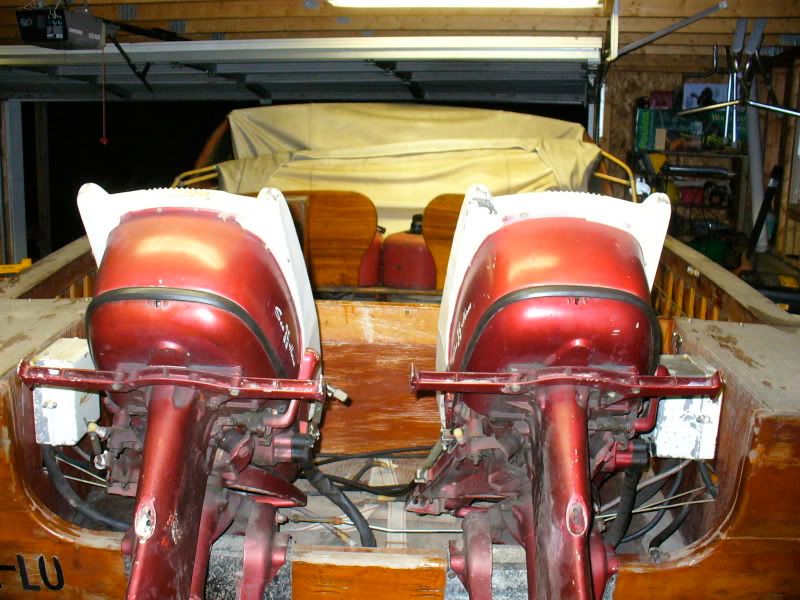
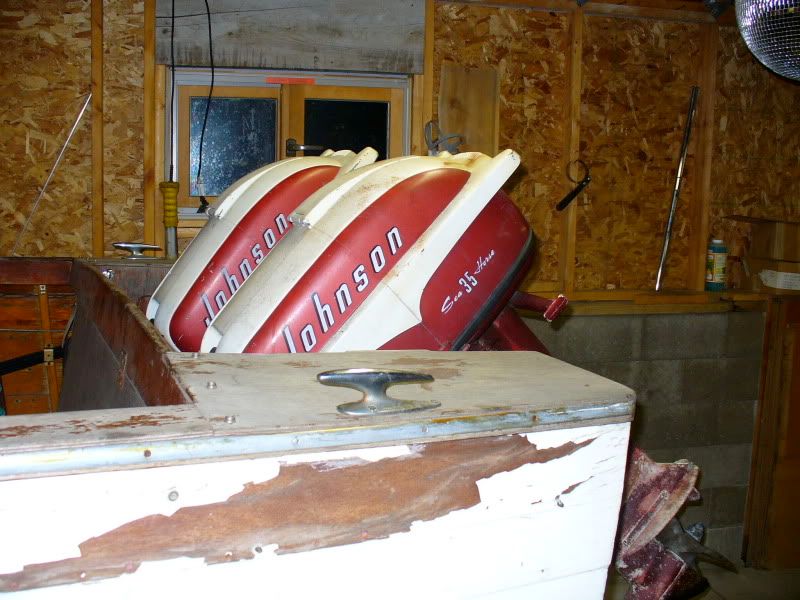
1. The project boat: 1955 Thompson Off Shore with twin 1957 35hp Johnsons. The lapstrakes on this boat are in great shape and since I don’t want to remove them I need to replace the ribs with the hull intact. Once the ribs are replaced the boat will be flipped and the entire hull stripped and painted.

2. This pic shows there was some rib issues. 12 ribs in all will be replaced. Some were cracked, some were rotted, some both.
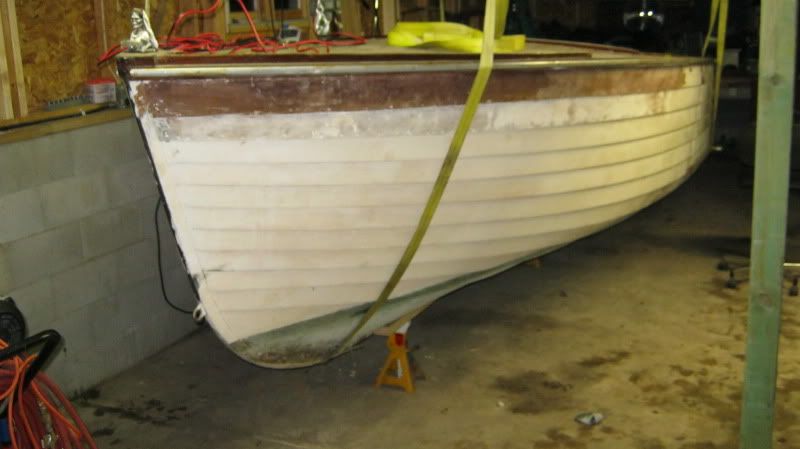
3. First task was to remove boat from trailer so that we have total access to hull bottom. In this pic the boat is on stands and timbers with the straps adding extra stability.
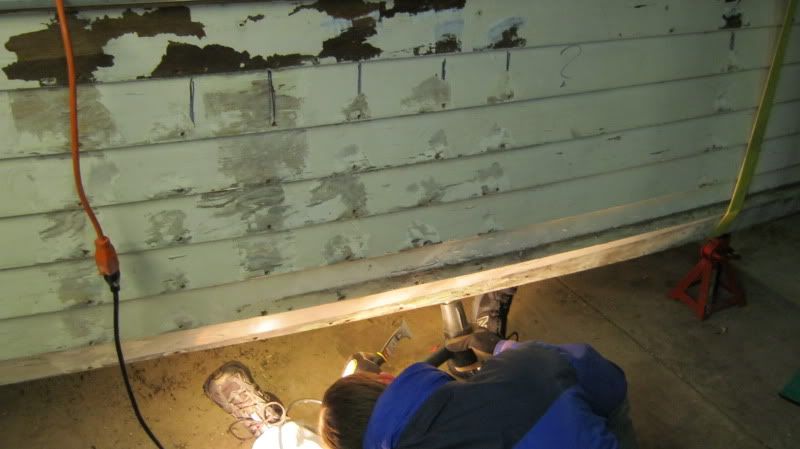
4. Screws that hold the ribs in are located, uncovered and removed.
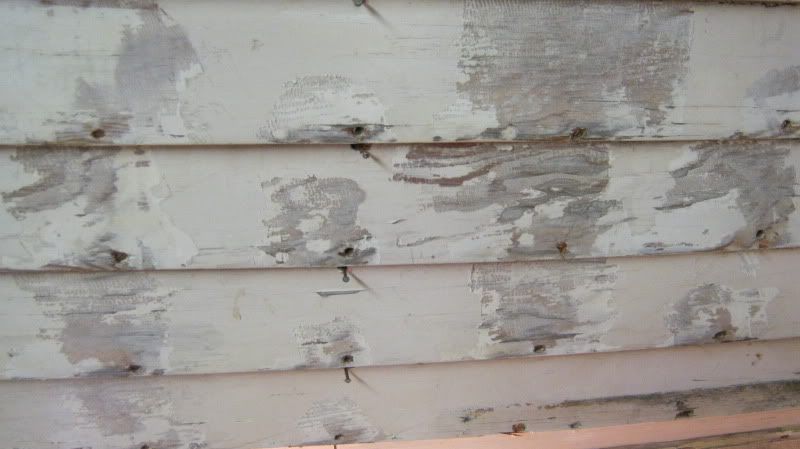
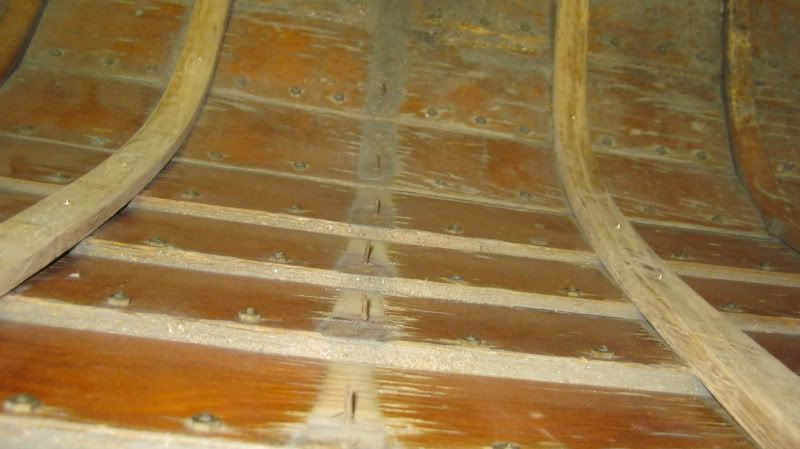
5. One rib had both screws and nails.
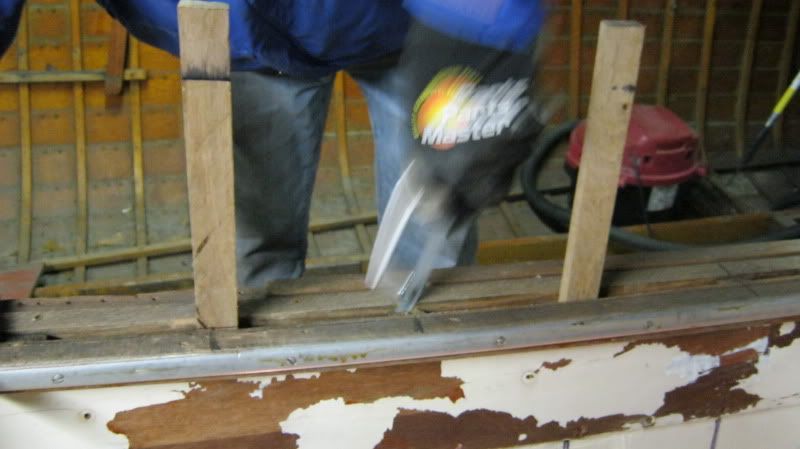
6. Some screws had to be cut. There are two screws that hold the rib to the gunnels. These can’t be removed without taking off the rub rail and the inner trim board, which we left on to help the hull retain its shape. These two screws will be replaced drilling thru the rub rail and the inner trim board. The rub rail screw will be covered by the aluminum rail trim and the trim board screw will be countersunk and bunged. There is also a screw at the bottom edge of the shear strake that can be removed.
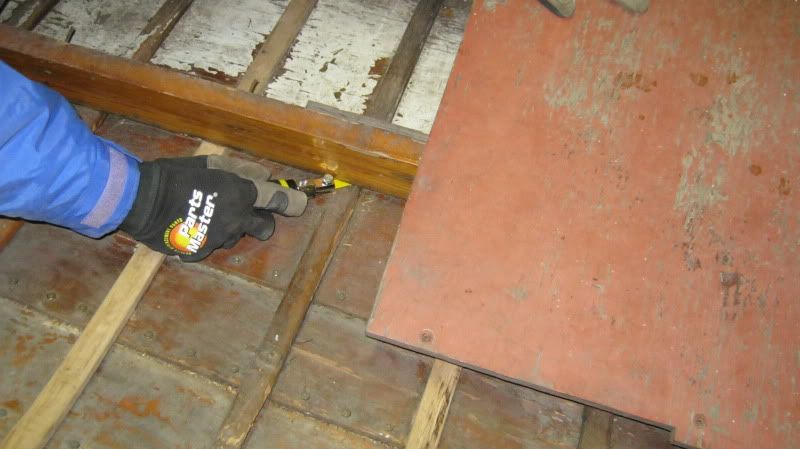
7. There is a screw or a nail going up thru the rib into the sister keelson. This will need to be cut as well.
This screw will be replaced from underneath by going thru the lapstrake or garboard, thru the rib and into the sister keelson. You will need to make some notation as to where the location of this screw needs to be. I used the nearest existing screw hole as my measuring point.
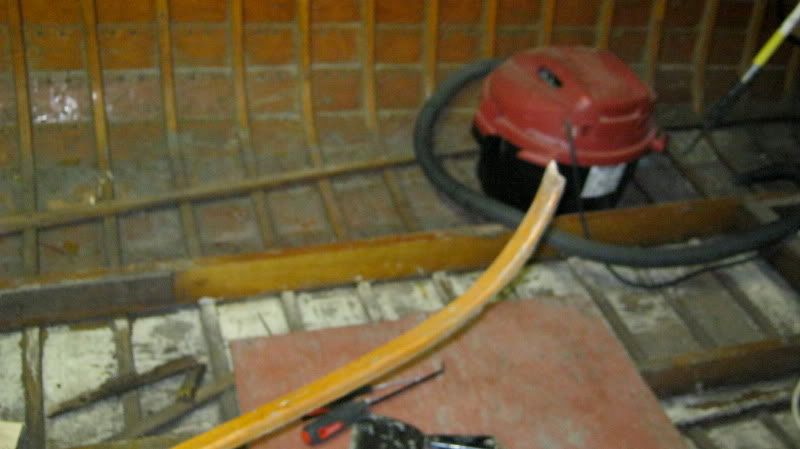
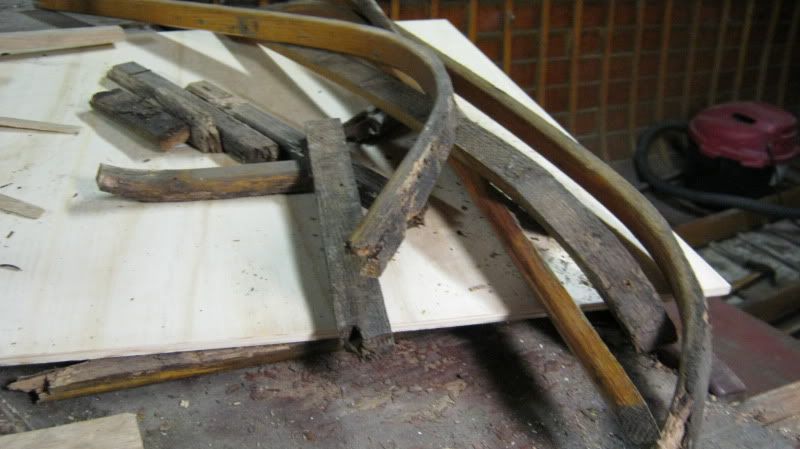
8. Remove the old rib. It will usually look something like this.
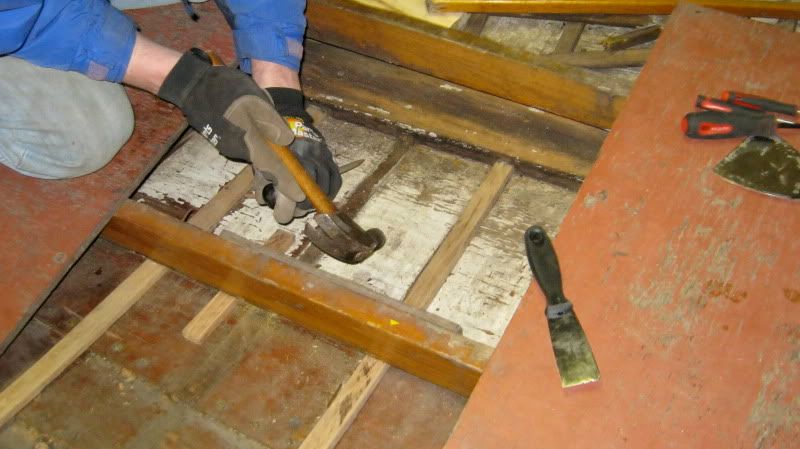
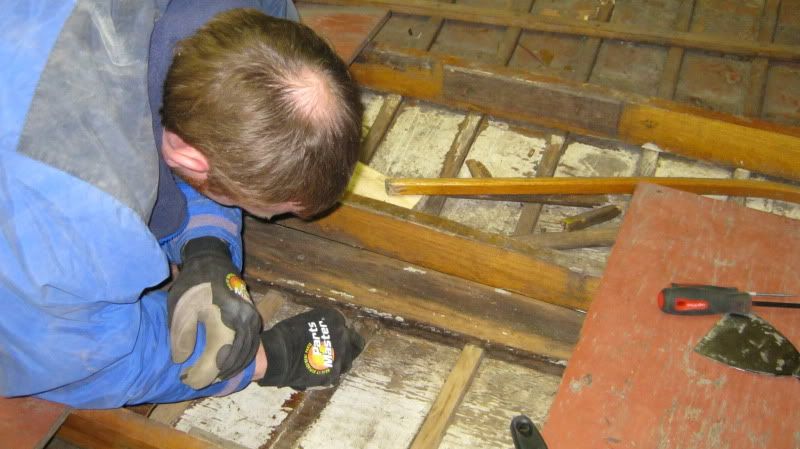
9. The keelson on the Off Shore is notched and the ribs fit into this notch . All of the old rib has to be removed so that the new rib can be forced into this notch and screwed to the keelson thru the bottom. I believe that this system of rib/keelson connection may be particular to the Off Shore models. This part of the process took the most time. We used a small chisel and pick and LOTS of patience. The ribs MUST attach to the keelson for structural integrity.
10. New ribs were milled from an 8’ piece 5/4 white oak that was quarter- sawn. I used quarter sawn as I noticed that many of the original ribs had grain markings that looked like quarter -sawn oak. The original ribs may have been “rift” sawn but that option was not available to me.
The ribs on my boat are 5/8 thick X 1-1/8 wide. After cutting the stock on a table saw I used a palm sander to profile the edges that are exposed. I then inspected the rib again for graining, knots, imperfections , etc. and trimmed them down to 6’ lengths.
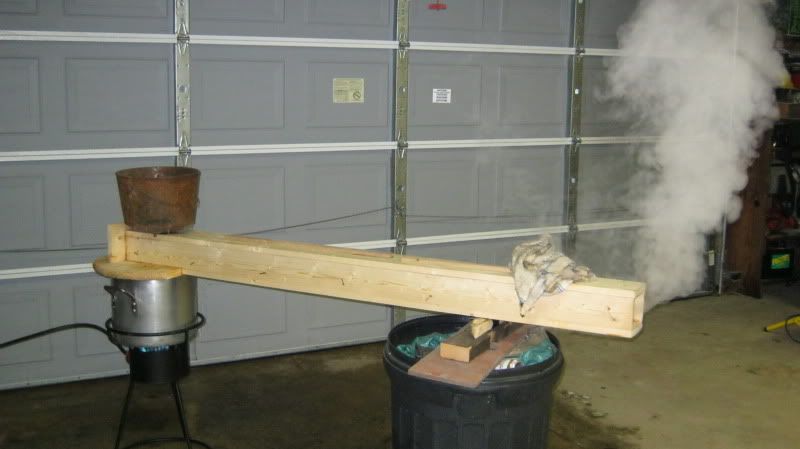
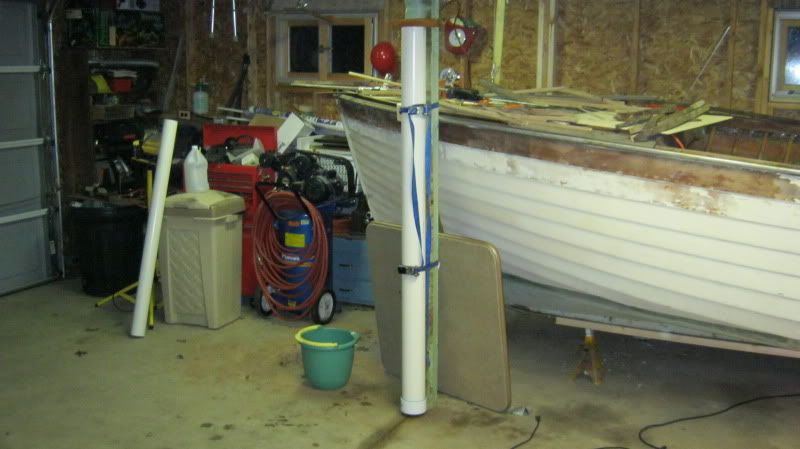
11. This is the steamer that I built. I use a borrowed Turkey fryer for the heat source. Three gallons of water will last about 3 hours. I stuff a rag into the end of the chamber but still allow steam to flow out the end. You need to maintain 212°F thru out the steaming process – boiling temp. I steamed my ribs 35 minutes based on the formula of 1 hour / 1” thickness. I soaked the ribs for 2 days in a PVC tube with an end cap on the bottom that I lashed to an upright post in the garage. I used salt water to soak the ribs because that’s the way I was taught plus salt water won’t freeze solid in my Northern Michigan garage when the heat is off.
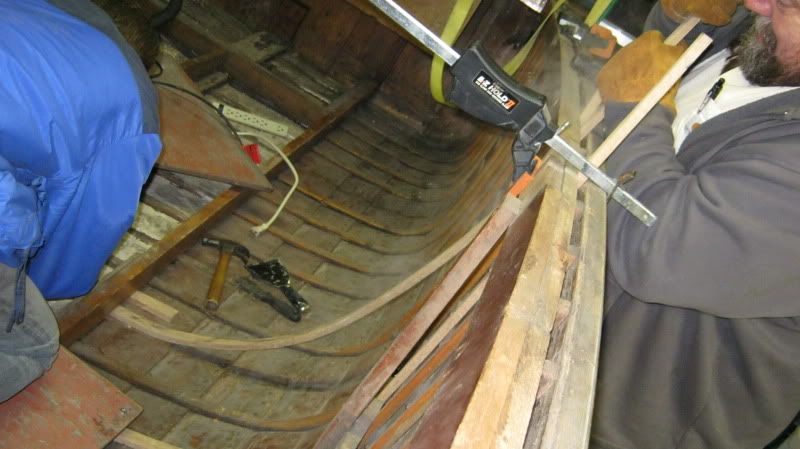
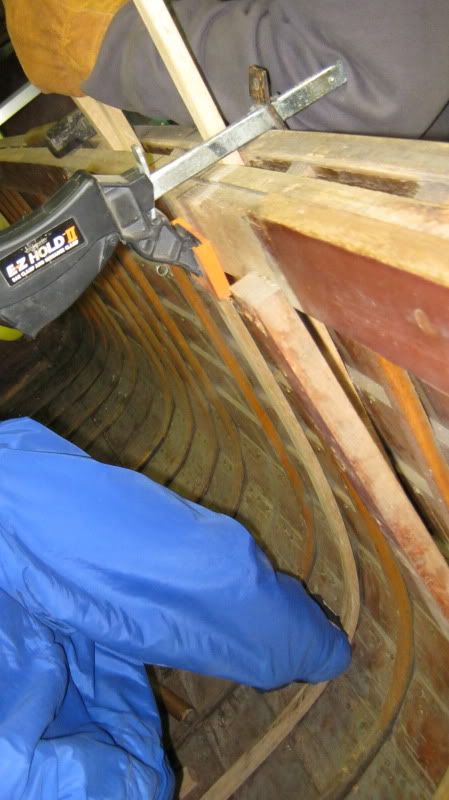
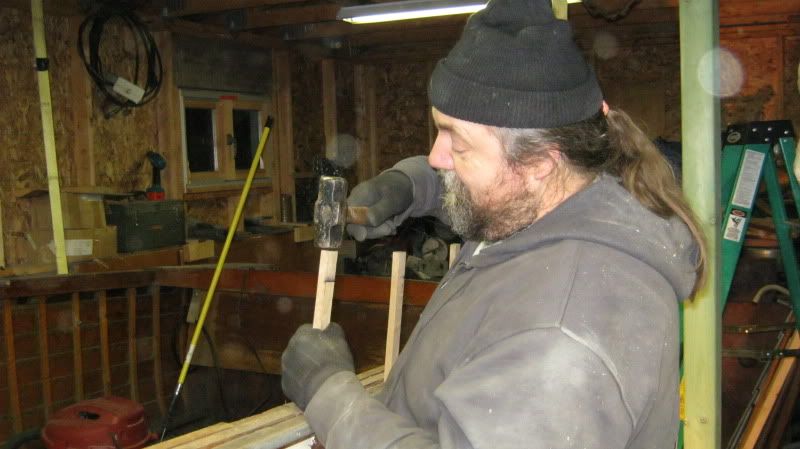
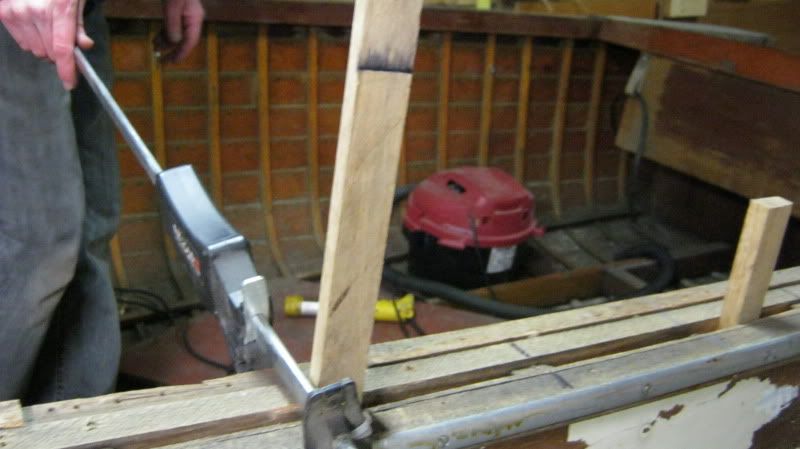
12. Bending and installing is a 2-person operation. One person in the boat and one person out.Wear heavy gloves to protect from the steam.
Steam the ribs for 35 minutes. Remove and quickly insert between gunwale and inner trim board forcing the rib down. As you do this the person inside the boat starts to bow the rib guiding the end over the edges of the lapstrakes and under the sister keelson and into the notch in the keel. At this point the inside person is pressing on the rib to make sure that it is in contact with the side and curve of the hull. The outside person uses a big hammer to pound down on the end of the rib to force the rib into the keelson notch and to help to set it completely against the curve and side of the hull. Once everything is in place clamp the rib securely at the gunnels and start to replace the thru hull screws. I start at the bottom lap and come up at least around the curve of the hull. Then I do every other lap just to make sure the rib is tight to the side of the hull.
This whole process should take around a minute.
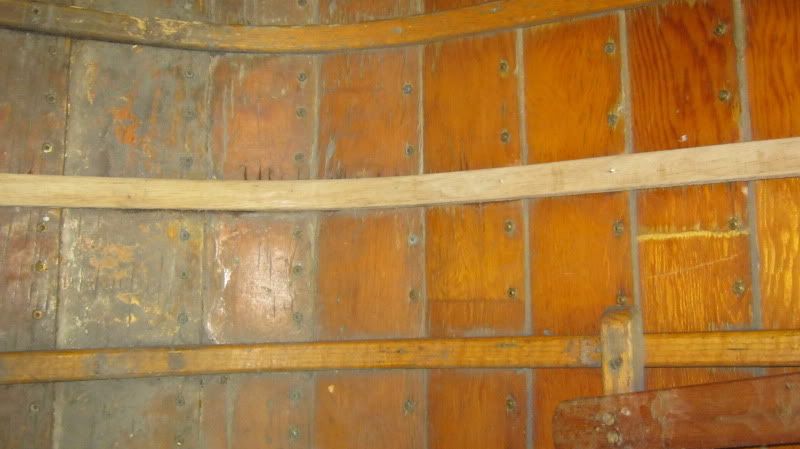
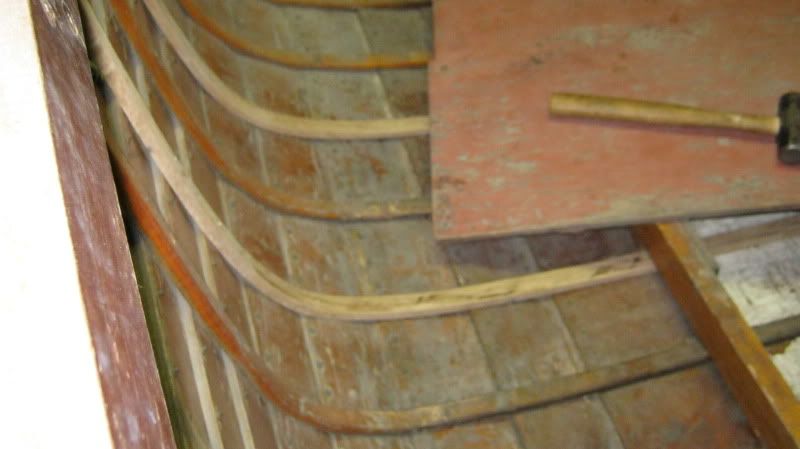
13. New ribs in place
14. Here are a couple of more pics - my best helpers and my boat towing vehicle - Karl
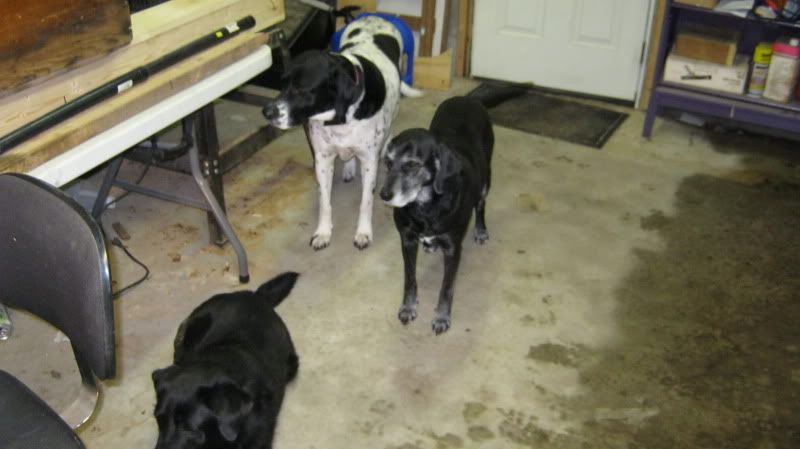
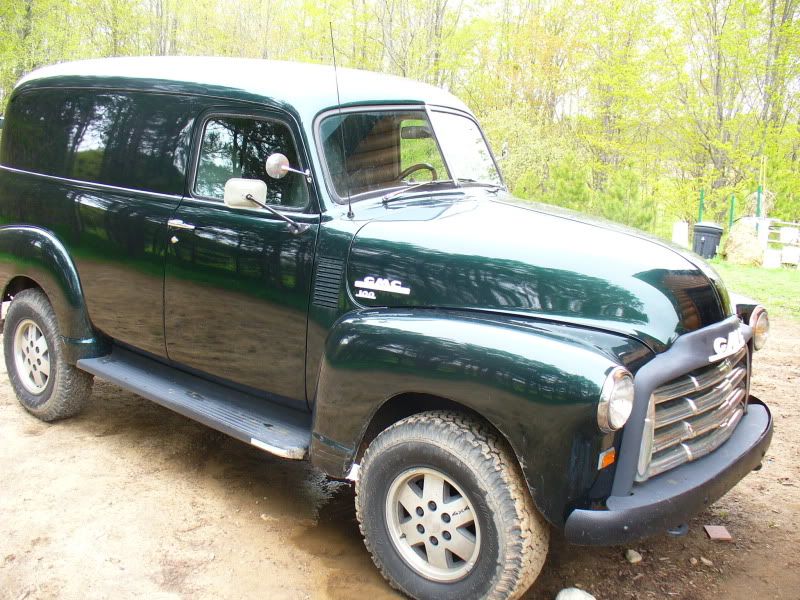